Durante le attività di ricerca per l’ottimizzazione del fascio neutronico per i pazienti di BNCT a partire dalla tecnologia INFN (fascio di protoni da 5 MeV su target di Be) è risultato evidente che il materiale più vantaggioso per ottenere uno spettro con basse contaminazioni è il fluoruro di alluminio. Tuttavia, questo materiale esiste solo in polveri, che difficilmente si possono compattare fino alla densità nominale e soprattutto non garantiscono stabilità e uniformità. Si è deciso quindi di studiare un metodo di densificazione basato sulla sinterizzazione. La sinterizzazione è un processo che permette la densificazione rapida di materiali ad alta temperatura, in presenza di pressione uniassiale.
La tecnologia messa a punto a Pavia è caratterizzata da un sistema di alimentazione ottimizzato e da una particolare conformazione degli stampi per la compressione delle polveri. Inizialmente è stato costruito un prototipo (nell’ambito del progetto INFN finanziato dalla CSN5, BEAT_PRO e del progetto di grande Rilevanza NEU_BEAT finanziato dal MAECI nell’ambito del Programma di Cooperazione scientifica e tecnologica con la Cina 2016-18). In seguito, dopo aver dimostrato il funzionamento della tecnologia secondo le specifiche, si è deciso di migliorare la macchina e creare uno strumento polivalente, più efficiente e meno costoso di quelli commerciali, di possibile interesse per laboratori e industrie che necessitano di manufatti di piccole e medie dimensioni. Questa nuova macchina è stata progettata e costruita presso l’officina meccanica della Sezione INFN di Pavia in collaborazione con il Dipartimento di Chimica dell’Università di Pavia, e finanziata nello schema R4I dell’INFN (2019). La macchina costruita è stata ingegnerizzata per risultare più compatta, più versatile, dotata di un numero di sensori più elevato, che permetta la sinterizzazione di campioni di maggiori dimensioni e con un raffreddamento più efficiente. Inoltre, è stato disegnato un carter di copertura che la rende esteticamente più gradevole e soprattutto più sicura. La foto mostra la macchina attualmente in uso nel Laboratorio di Tecnologie Avanzate attiguo all’officina meccanica della Sezione di Pavia.
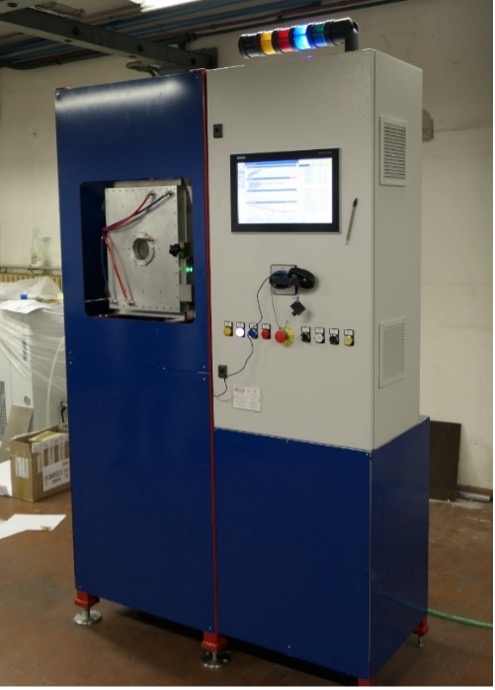
foto: TT_SINTER
La tecnologia di sinterizzazione proposta è risultata imprescindibile non solo per la produzione di materiali densificati per moderazione neutronica. Un nuovo materiale costituito da polveri di fluoruro di alluminio e fluoruro di litio (che serve a rimuovere la componente termica dei neutroni nel fascio) è stato sinterizzato e denominato Alliflu. La foto sottostante mostra l’interno della camera a vuoto di sinterizzazione fotografato dall’oblò, con la pressa di grafite incandescente durante un ciclo di sinterizzazione di Alliflu.
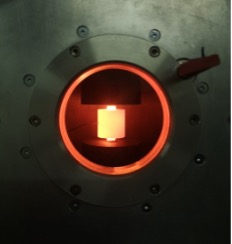
Foto: un momento del ciclo di sinterizzazione all’interno della camera di TT_SINTER
Sono stati così prodotti elementi solidi di diversi diametri, adatti alla costruzione di un assembly per la moderazione del fascio neutronico (foto)
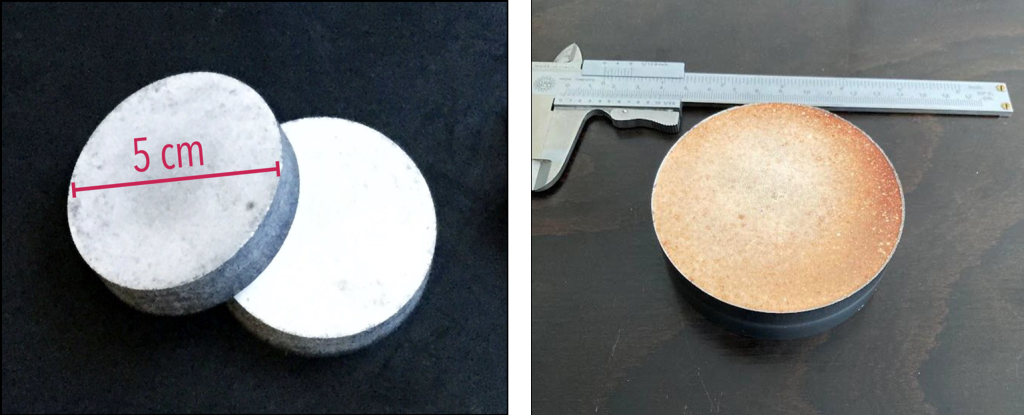
Foto: elementi sinterizzati di Alliflu di 5 e 8 cm di diametro
Questa tecnologia sarà utilizzata per la costruzione del moderatore del fascio per il centro BNCT di ANTHEM (link alla pagina del sito su ANTHEM). TT_SINTER si è dimostrata una tecnologia adatta anche per la sinterizzazione di elementi di fluoruro di magnesio, e attualmente stiamo producendo elementi esagonali per l’Università di Granada nell’ambito di una collaborazione conto terzi (foto).
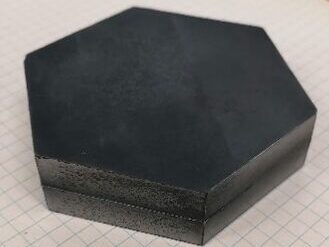
Foto: elemento esagonale di fluoruro di magnesio (dimensioni vertice-vertice:8 cm, spessore: 2 cm)
TT_SINTER si è dimostrata anche una tecnologia adatta alla produzione di target multistrato per ottenere radioisotopi medicali attraverso irraggiamento con protoni. Questa attività con TT_SINTER è stata esplorata dai ricercatori del progetto Laramed a LNL, e infatti una seconda macchina con le stesse caratteristiche è in via di completamento per i Laboratori. Dal momento in cui il nuovo prototipo è entrato in funzione, i colleghi di LNL sono venuti a Pavia per produrre target di diversa natura, nell’ambito delle sigle di CSN5 Remix e Cuprum. I target hanno dimostrato ottime caratteristiche meccaniche e i risultati sono stati mostrati a diversi congressi.
Grazie alle collaborazioni di Laramed nel campo della produzione di radioisotopi per uso medicale, un gruppo di ricerca dell’Università di Winsconsin-Madison (USA), ha dimostrato interesse nell’acquisire un esemplare di TT_SINTER. Dopo diversi scambi di informazioni, il responsabile del gruppo che si occupa di questa tecnologia a Madison è venuto a Pavia per produrre alcuni target di difficile realizzazione. Le performance di TT_SINTER si sono rivelate anche migliori del previsto, e i target testati sotto fascio hanno mantenuto le caratteristiche attese. Per questo, il gruppo di Madison ha deciso di acquistare una macchina e grazie alla consulenza del Servizio TT dell’INFN abbiamo trovato il canale corretto per effettuare questo trasferimento. Si è deciso di esternalizzare la costruzione della macchina a una delle ditte locali che erano state coinvolte per la produzione del prototipo attuale: Cometra di Roveda Marco, la quale a seguito della firma di un contratto con INFN (in cui si è definito il ricavo di INFN e si è sancita la proprietà del know-how), si è incaricata di tutta la costruzione fino all’assemblaggio (foto). INFN ha fornito assistenza a richiesta e si è occupata del test di funzionamento. La vendita a Madison è stata a cura di Cometra.
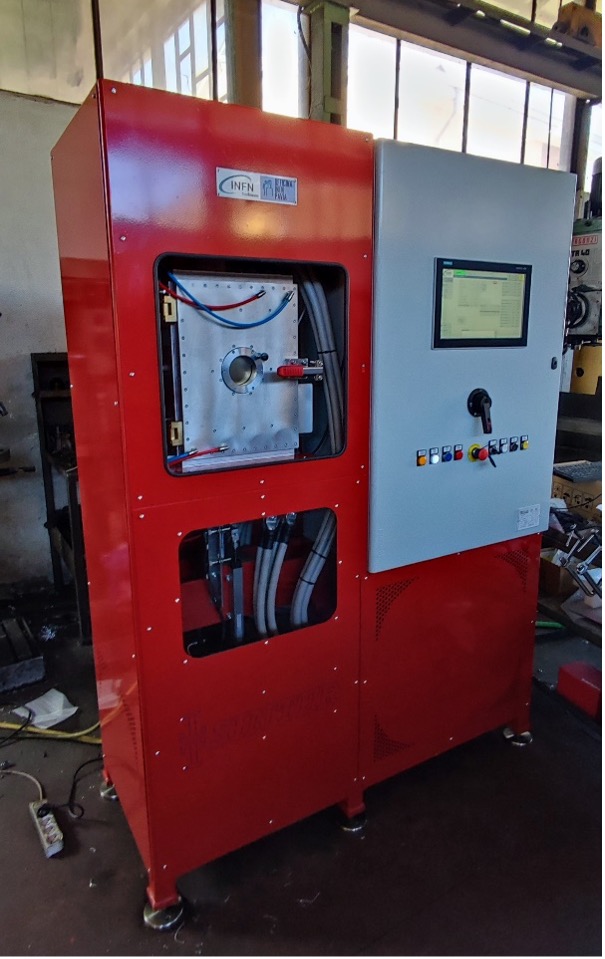
Foto – TT_SINTER per Università del Winsconsin-Madison (USA)
Prima di poter finalizzare la commercializzazione del prototipo è stata fatta la valutazione dei rischi e la preparazione del fascicolo tecnico da un soggetto esterno qualificato. Alla fine del processo di valutazione, TT_SINTER ha ottenuto la certificazione CE.
Il lavoro sulla produzione di materiali innovativi si è ulteriormente sviluppato con l’idea di accoppiare la sinterizzazione con la stampa 3D usando due diverse polveri, una che sinterizza e l’altra no, depositate con dispenser piezoelettrici. Questo permette di generare oggetti dalle geometrie complesse senza la necessità di costruire stampi. Questa idea è stata brevettata (nr brevetto 102021000011450, co-intestato INFN e Università di Pavia). Infine la realizzazione della tecnologia per applicare questa idea è stata finanziata per l’anno 2024 dal progetto PNRR Inteff (call Proof Of Concept), progetto X_FORM.